In various systems of automotive electronics, microcontrollers (MCUs) are often used as the core of operational control, and the reliance of automobiles on electronic systems also stimulates the rapid growth of the automotive microcontroller market. Microcontrollers for cars cover 8-, 16-, and 32-bit low-, medium-, and high-end product grades, each with its own suitable application system, roughly as follows:
8-bit MCU: mainly used in various sub-systems of the car body, including fan control, air conditioning control, wipers, sunroof, window lift, low-end instrument panel, hub box, seat control, door control module, etc. control function.
16-bit MCU: mainly used for power transmission systems, such as engine control, gear and clutch control, and electronic turbine systems; also suitable for chassis mechanisms, such as suspension systems, electronic power steering wheels, torque dispersion control, and Electronic pumps, electronic brakes, etc.
32-bit MCU: main applications include dashboard control, body control, multimedia information system (TelemaTIcs), engine control, and emerging intelligent and real-time safety systems and power systems, such as pre-crash, adaptive Safety functions such as cruise control (ACC), driver assistance systems, electronic stability programs, and complex X-by-wire transmission functions.
Common interface of MCU for car: CAN & LIN
As today's automotive requirements for application functions are getting higher and higher, the systems to be integrated are becoming more and more complex, making the demand for high-end 32-bit MCUs in automotive electronic systems increasing. Such vehicle MCUs are often placed in an operating environment with high heat, dust, shocks, and severe electronic interference, so the requirements for tolerance are much higher than general-purpose MCUs. In addition, in the automotive application environment, the automotive MCU must be connected to multiple automotive electronic control devices (ECUs), among which the most common transmission interfaces are CAN and LIN.
CAN is divided into high-speed CAN and low-speed CAN. The transmission rate of high-speed CAN can reach 1 Mbps, which is suitable for ABS, EMS and other applications that emphasize real-time response; low-speed CAN can reach 125 Kbps, which is suitable for lower speed car body parts control. In addition, the types of CAN controllers can be divided into the old 1.x, the standard 2.0A and the extended 2.0B. The newer the specifications, the better the performance. The 2.0B can be divided into passive (passive) and Active (acTIve) type.
LIN is a lower speed and lower cost communication solution than CAN. It adopts the concept of a master node and multiple slave nodes (supports up to 16 nodes), up to 20 kbps data transmission rate, and the length of the bus cable can be expanded to 40 meters. It is very suitable as climate control, mirrors, door modules, seats, smart switches, and low-cost sensors. Distributed communication solutions for simpler systems.
The following will introduce a new generation of MCU technology applied to dashboard control and body control, and take Fujitsu's new generation of MB91770 series and MB91725 series of new microcontrollers as design references. Please refer to (Figure 1).
Figure 1: The application of dashboard control and body control MCU in automobiles (taking MB91770 series and MB91725 series as examples)
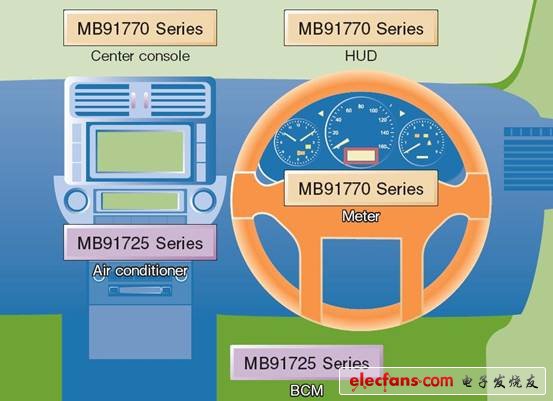
The main points of car dashboard and body control design
The dashboard of the car provides a variety of real-time visual information for the driver. This information is an important reference for assisting decision-making and must be quickly and accurately communicated to the driver. In addition, the air conditioning and body control module (BCM) system in the car is responsible for providing a comfortable ride environment for drivers and passengers. Among them, the optimal control of the air conditioning system quickly reduces the temperature inside the car to a more comfortable level, and maintains a comfortable interior temperature based on the information from various sensors. The BCM system can centrally control multiple ECUs, such as doors, seats, and combination switches.
Whether it is a dashboard control or body control MCU, it must provide higher processing performance, the ability to handle a large number of network nodes, interface functions that support multiple peripheral connections, functions that can expand the scope of circuit board layout, advanced memory architecture, And a more convenient development environment. The analysis of these design requirements is as follows:
High processing performance:
To improve processing performance, MCU must start from its core and software and hardware system architecture. Take Fujitsu's new generation MCU FR81S CPU core as an example. Its working performance reaches 1.3MIPS / MHz, which is 30% higher than the previous generation FR60 core. Efficiency; due to the built-in single-precision floating-point arithmetic unit (FPU), it can meet the requirements of image processing systems and those systems that require floating-point operation functions (such as brake control). In addition, through hardware-based FPU support, it can simplify software programs and improve computing performance.
Safety Light Curtain,Safety Curtain,Laser Safety Light Curtain,Safety Optic Light Curtain,Security Light Curtain,Press Brake Safety Light Curtains
Jining KeLi Photoelectronic Industrial Co.,Ltd , https://www.sdkelien.com