1 Overview
This article refers to the address: http://
The exterior mirror is one of the important devices for active safety of the car. It is a tool for the driver to obtain external environmental information such as the sides and rear of the car, and is also an important tool to ensure the safety of the car. During vehicle driving, road excitation, engine and transmission system vibrations can cause body vibrations, which can cause different degrees of jitter in the rearview mirror. Severe jitter can cause unclear rear view, causing the driver to cause a traffic accident due to misjudgment. According to the statistics of the literature, traffic accidents caused by defects in the design and manufacture of rearview mirrors account for 30% of the total number of traffic accidents, while the proportion of the United States is 20%, especially on highways, which is as high as 70%. Therefore, in addition to meeting the relevant regulations and standards, the rearview mirror must carefully select the curvature radius, the mirror size, and the installation position, and must pay attention to the dynamic characteristics of the rearview mirror.
2 Proposal of the problem
During the road test of a passenger car in China, it was found that the rear view mirror not only experienced severe jitter under idle conditions, but also had significant jitter on high-speed driving and rough roads. The driver's observation of the blurred vision is not only easy to cause the driver's visual fatigue, but also can not accurately and accurately determine the situation on both sides and the rear, there is a large potential safety hazard. This article has analyzed and improved this issue.
3 Experimental modal analysis
In order to obtain the real working condition of the rearview mirror, the test is carried out on the whole vehicle, and the dynamic characteristics of the rearview mirror are tested by hammering excitation. The data acquisition front end of the experiment adopts SCADIII of LMS company, the hammer uses HEV200 of PCB company, the sensor adopts the three-way acceleration sensor of PCB company, and the data analysis and processing software adopts Test.LAB 9 and so on.
The position of the sensor is shown in Figure 1.
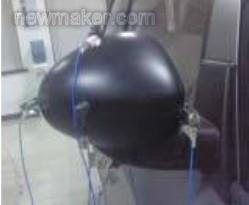
Figure 1 Rear view mirror sensor placement position
The data acquisition cutoff frequency is 512 Hz and the frequency resolution is 0.5 Hz. The following results can be obtained through analysis:
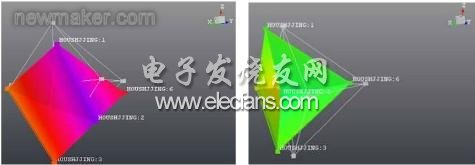
Figure 2 Mirror modal calculation results
From the test results, the modal frequency of the rearview mirror is low, which is easily excited by the engine, the transmission system and the road surface, which is an important cause of the mirror shake.
4 Rear view mirror numerical simulation analysis
In view of the problem of the rear view mirror shake that occurs in this vehicle, it is difficult and time consuming to simply use the test method to find the cause of the problem. In order to quickly find out the design defects of the structure and propose modifications, this paper uses the simulation method to analyze the structure modality of the rearview mirror structure, check out the problems existing in the structure, and propose suggestions for changes.
4.1 Establishment of finite element model
In order to make the rear view mirror modal analysis under the condition of close to the actual situation, the rear view mirror is installed in the state of the front door for analysis. The finite element model of the rear view mirror and the front door is completed in HyperMesh, in the finite element. In the model, the tetrahedral element TETRA4 is used. The unit of the sheet metal part is divided into quadrilateral elements CQUAD4, the transition unit is triangular unit CTRIA3, and the control is within 3%, the hinge axis is simulated by RBE2 unit, and the solder joint is performed by CWELD unit. Simulation and glue are simulated using solid elements. The finite element model is shown in Figure 3:
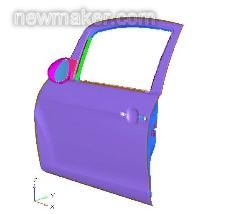
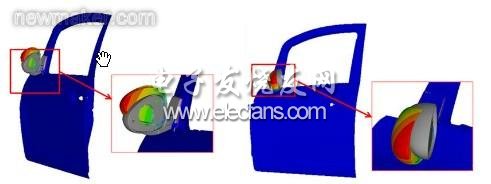
Figure 4 Modal finite element analysis results of the rearview mirror
After the finite element model is completed, the material properties are respectively assigned, and the constraints are imposed on the model. The constraints are processed according to the actual working state of the door, the degree of freedom of the three directions of the door lock and the hinge is constrained, and the side door and the side are constrained. The Y-direction translational freedom of the contact area, when these settings are completed, is then submitted to RADIOSS for calculation. The calculation results are shown in Figure 4 below.
In order to clearly understand the compliance of the finite element analysis and the test, the results of the two are compared, as shown in Table 1 below. It can be seen from Table 1 that the difference between the test results and the finite element analysis results is small, indicating that the simulation analysis results have higher credibility, so the improvement of the structure can be realized by the finite element simulation method.
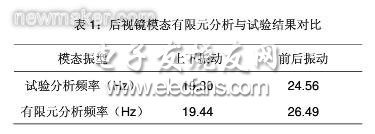
4.2 Design modification and verification analysis
It can be seen from the above test and analysis that the main reason for the rear view mirror shake is that the frequency of the vertical vibration is low, and increasing the frequency value of the mode is an important target of this modification. Using the optimization analysis of Hyper study and the structure of similar rearview mirrors, two factors have an important influence on the calculation results [3]: First, the material properties of the triangle seat (see Figure 5) have a greater influence on the modality. The material is PA6, and the modulus of elasticity is small. By confirming with the supplier, it is possible to increase the modulus of elasticity of the material by adding glass fiber (GF) and metal powder (MD), thereby increasing the modal frequency of the mirror.
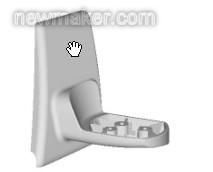
Figure 5 Rearview mirror tripod
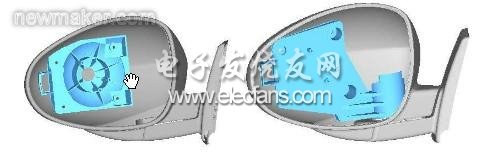
Figure 6 Comparison of the structure before and after the modification of the rearview mirror
Secondly, due to the structural characteristics of the interior glass bracket of the rearview mirror, the bracket is only connected to the mirror housing (see Fig. 6(a)), and is not connected to the triangular bracket, and the mass of the bracket is large, resulting in the center of gravity of the rearview mirror. The overall orientation is outward, forming a structure similar to a cantilever beam, making the rear view mirror more susceptible to vibration. To this end, the structure has been modified, and the modified structure is shown in Figure 6(b).
Complete the above modifications, re-modeling for finite element analysis, and the results of the analysis are shown in Table 2 below. It can be seen from Table 2 that the modified first-order up-and-down vibration frequency is increased to 34.24 Hz, and the second-order front-end vibration frequency is also increased to 40.53 Hz, effectively avoiding the resonance frequency of the excitation source, and basically meets the design requirements. In the subsequent road test, the rear view mirror did not appear to be shaken, indicating that the above modification effect is indeed effective.
Table 2 Results of finite element analysis of rearview mirrors before and after modification
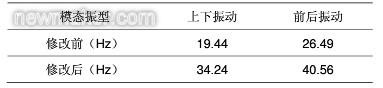
5 Analysis and conclusion
In view of the situation that the rear view mirror shakes in a certain domestic car, the reason for the jitter is found through experiments. In order to quickly find the defects of the structural design and the improved method, through the establishment of the finite element model in Hypermesh and the multiple analysis by RADIOSS, the design defects of the rearview mirror jitter were found, and the modification of the part material and the part structure was The angle has been modified, and the modified rearview mirror has no jitter, which provides a solution to the problem of rearview mirror shake.
Winnowing Machine,Winnowing Rice,Seed Winnowing Machine,Grain Winnowing Machine
Hunan Furui Mechanical and Electrical Equipment Manufacturing Co., Ltd. , https://www.frcornthresher.com