In the absence of a grounding line selection device in the substation, or if there are no ground fault indicators or combined short-circuit and ground fault indicators on the line, and no effective ground fault detector is available, manual searching becomes the only option. This method is time-consuming and inefficient. The process typically involves manually or through scheduling, disconnecting switches one by one to identify which outlet is grounded and which phase is affected. There are two common approaches to locate the fault: first, segmenting the line step by step, or targeting frequently faulty sections, using a 2.5kV megohmmeter to measure insulation resistance relative to ground. A low reading indicates a fault. Once identified, the search area can be narrowed down, but proper safety measures such as grounding must be taken on the substation side. Alternatively, the line can be segmented as much as possible, and power can be restored step by step while coordinating with dispatch. If a zero-sequence voltage alarm occurs, that section is likely the fault location.
Manual methods are laborious, especially when dealing with long lines, numerous branches, or limited switch segmentation. Poor weather conditions can further complicate the process. It is recommended to combine manual efforts with some cost-effective technological tools to improve efficiency, enhance power supply reliability, and generate both social and economic benefits.
If a grounding line selection device is installed, it can provide guidance for manual operations. Installing ground fault indicators (or combined short-circuit and ground fault indicators) along the line helps detect fault paths. Currently, the most reliable detection method is the signal source approach, while the first half-wave method or DC transient analysis is more sensitive. Using a combination of these methods—primarily the signal source method with supplementary techniques like the first half-wave or DC transient analysis—is recommended for better performance.
For users with the budget, feeder automation offers a more advanced solution. This method uses intelligent switches (such as load switches, sectionalizers, circuit breakers, reclosers with FTUs) to automate fault isolation, recovery, and power transfer. For example, on a dual-power supply hand-in-hand line divided into six segments with five intelligent switches, the fault point can be isolated automatically. The steps include: the substation disconnecting the grounded outlet, followed by automatic opening of each segment’s intelligent switch. Then, the substation re-energizes the line. If the zero-sequence voltage does not trigger an alarm, the segment resumes power. The first intelligent switch detects the line voltage but not the zero-sequence voltage, then closes after a delay. If a zero-sequence voltage is detected, it opens and locks. The second switch also detects the voltage but remains locked. The middle switch detects a single-side power loss and auto-closes after a delay. If no zero-sequence voltage is present, the segment is successfully transferred. Finally, the second intelligent switch detects the line voltage but remains open due to the lock, isolating the faulted section while restoring power to non-faulty areas.
Changing the neutral point grounding method can also help. Systems using ungrounded or arc suppression coil grounding have their own advantages and disadvantages. To address the challenges of fault detection and safety issues, users often consider two main options:
1. Changing the neutral point to a small resistor grounding. After this change, the zero-sequence two-stage protection and the short-circuit indicator of the circuit breaker can solve about 70% of ground fault problems, though 30% of medium and high-resistance faults may still remain. In such systems, digital fault indicators that monitor zero-sequence current, total line current, and grounding insulation voltage (for overhead lines) can send data through a communication network to the dispatch system for real-time and historical analysis, helping to pinpoint the fault location.
2. Implementing a small resistance or medium resistance grounding mode with a circuit breaker or high-voltage contactor. These devices normally stay in the off position and only close after detecting a rise in zero-sequence voltage. They act as temporary resistors during short periods, allowing the same detection methods used for small resistance grounding to locate the fault. Additionally, the flexibility of controlling the neutral point resistance allows the protection device or ground fault indicator to recognize the signal and indicate the fault path after the arc suppression coil is activated.
Push Button Switch
Push Button Switches
The Push Button Switches, also known as the control button (referred to as the button), is a low-voltage electrical appliance that is manually and generally can be automatically reset. The Push Button Starter Switch is usually used to issue a start or stop command in the circuit to control the turning on and off of electrical coil currents such as electromagnetic starters, connectors, and relays.
The On Off Push Button Switches refers to a switch that pushes the transmission mechanism with a button to make the movable contact and the static contact open or close and realize circuit switching. It is a master control device with a simple structure and a wide range of applications. In the electrical automatic control circuit, used to manually send control signals to control connectors, relays, electromagnetic starters, etc.
This Pushbutton Switches is a kind of electric device that is used to switch on and off the small current circuit when the action is released. Generally used in AC and DC voltage below 440V, the current is less than 5A in the control circuit, generally do not directly manipulate the main circuit can also be used in the interconnection circuit. In actual use, in order to prevent desperation, different marks are usually made on the buttons or painted with different colors, and the colors are red, yellow, blue, white, black, green, and the like.
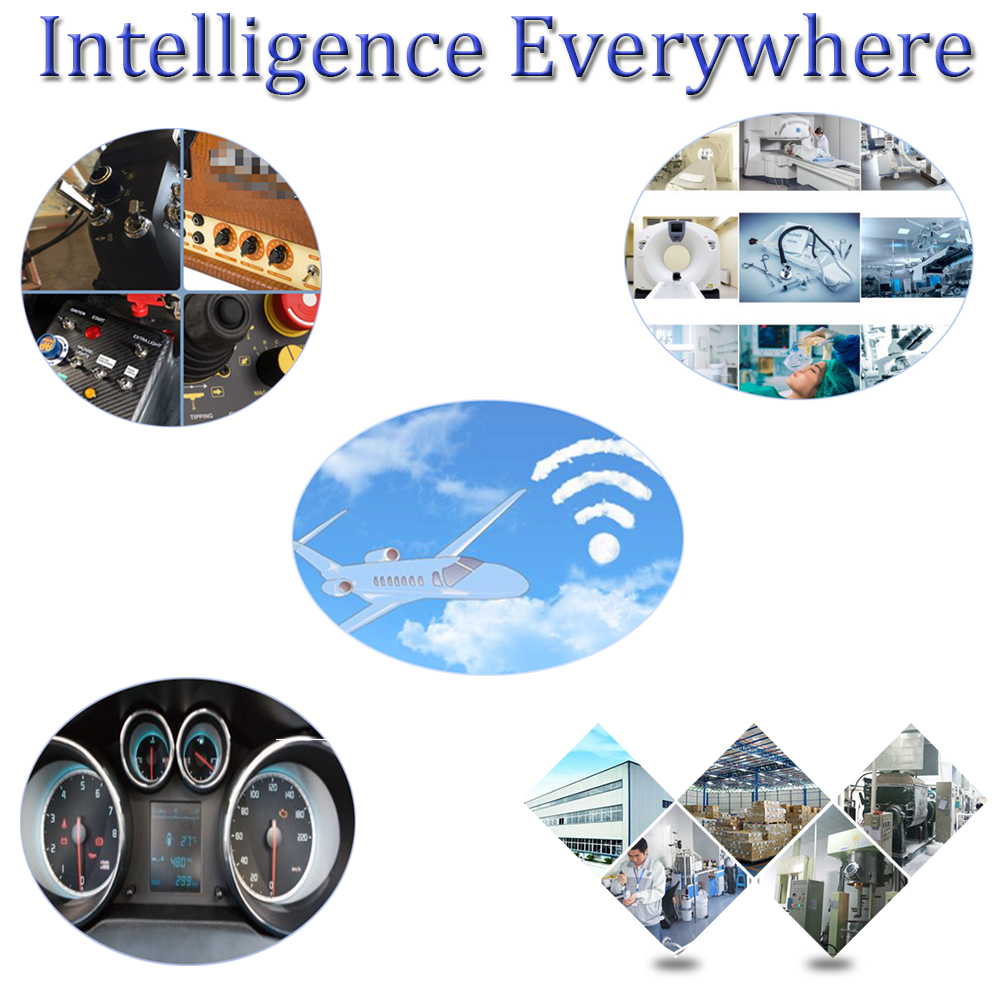
The Momentary Push Button Switch could be divided into metal push button switches and LED Light Switches and ordinary snap button type, mushroom head type, self-locking type, self-resetting type, rotary handle type, with indicator light type, lighted symbol type and key type, etc., with single button and double Buttons. Generally, it adopts a water-storage structure, which consists of a button cap, a return spring, a static contact, a moving contact and a casing. It is usually made into a composite type, and has a pair of normally closed contacts and normally open contacts, and some products can pass. The series connection of multiple elements increases the number of contact pairs. There is also a self-contained button that automatically holds the closed position when pressed, and can be turned on only after the power is turned off.
When the Metal Switches is not pressed, the movable contact is connected with the upper stationary contact. The pair of contacts is called a normally closed contact. At this point, the movable contact is disconnected from the following static contact. The pair of contacts is called a normally open contact: the button is pressed, the normally closed contact is open, the normally open contact is closed, and the button is released. Restore the original working state under the action of the return spring
Push Button Switches,Push Button On Off Switch,High Button Switch,Push Button Switch Types,Pushbutton Switches,Lock Push Button Switch,Momentary Push Button Switch,Sub-miniature Push button Switch,Sealed Push button Switch
YESWITCH ELECTRONICS CO., LTD. , https://www.yeswitches.com